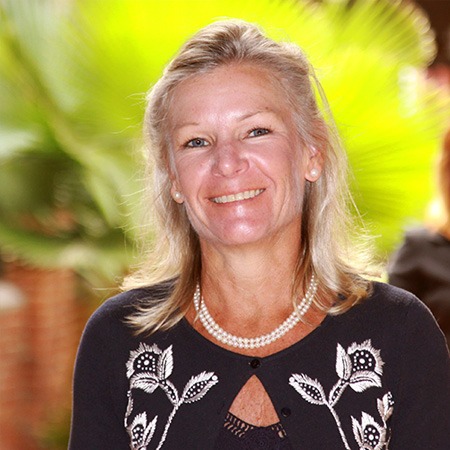
Kathy Webb, P.G.
Senior Market Leader | Principal
Kathy Webb, who co-founded SynTerra (then known as The Fletcher Group) in 1992, has completed remedial investigations and regulatory compliance projects associated with Resource Conservation and Recovery Act (RCRA) facilities, state and federal Superfund sites, solid waste landfills, brownfield redevelopment, utility coal combustion residual (CCR) management units, and regulated industrial facilities. She has supported litigation as an expert witness related to chlorinated solvents, metals, and polychlorinated biphenyls (PCBs).
Kathy is known for her practical assessment strategy with the perspective of the client’s business objectives. She routinely evaluates groundwater corrective action systems for effectiveness and progress toward achieving compliance objectives. She has co-authored a trade journal paper with case studies of low-impact remedial strategies. Kathy is a licensed Professional Geologist in North Carolina and South Carolina.